In order to achieve a given degree of hydrogen concentration and remove impurities, the process uses numerous adsorption layers. In PSA unit, converted hydrogen- bearing gas is purified from methane and carbon oxides impurities by adsorption of contaminants on the adsorbent at high pressure and desorption at low pressure.
Feed used for hydrogen production is hydrogen-bearing gas with hydrogen concentration of about 75-80% vol. The products are hydrogen with concentration above 99.5% vol., as well as stripping gas with hydrogen content of 10-40% vol.
Application
- Oil refining processes
Extraction and concentration of hydrogen in oil refining cycles. Concentration of hydrogen from stripping gases of hydrotreating, hydrocracking, isomerization, catalytic reforming, reducing the concentration of undesirable impurities to the required level.
- Chemical and petrochemical processes
Extraction and concentration of hydrogen from stripping gases of pyrolysis, dehydrogenation of alkanes and alkenes, stripping gases of methanol production and other process streams.
- Ammonia production
Separation of hydrogen from nitrogen, methane and argon in ammonia purge gas streams.
- Syn gas production
Production of high-purity hydrogen from syn gas with almost complete removal of CO and CO2.
Scope of Equipment
- Pressure vessels:
• combined fine purification separator;
• product hydrogen filter (optional).
• adsorber;
• residual gas tank with internal devices.
- Compressor system:
• residual gas compressor (optional). Screw compressor for supplying residual gas to the fuel ring;
• screw compressor on the assembly stand;
• preassembled screw compressor unit.
- Valve assembly with instrumentation and pipelines
- Safety valves to protect the unit against overpressure
- Control system
- Control software
- Ladders and service platforms, pipelines outside valve assembly
- Specially selected adsorbent
Advantages
- Extensive experience of our specialists in design and commissioning of PSA Unit (more than 1000 units)
- High product recovery rate
- Automatic start from “zero” pressure. All preliminary start-up operations are performed automatically
- Decommissioning of unit in automatic mode without shutting it down with maintaining product purity and its recovery rate
- Specially selected switching valves with high number of actuation cycles
- Specially selected adsorbent with service life of 15-20 years
- For reliable operation in winter period, all valves are equipped with heat insulation casings with electric heating. At Client’s request, the entire valve assembly can be placed in a shelter with heating and ventilation
Basis of PSA process
Pressure swing adsorption process is based on physical adsorption phenomena, where highly volatile compounds with low polarity (hydrogen or helium) are practically not adsorbed compared to molecules of CO2, CO, N2 and hydrocarbons. Consequently, most impurities in hydrogen-bearing stream can be selectively adsorbed to recover high-purity product hydrogen.
PRESSURE SWING ADSORPTION (PSA) unit is designed for continuous purification of HBG. Although PSA process appears to be continuous on the outside, internally it is interrupted, consisting of many sequences running in parallel. In general, each adsorber performs a special PSA cycle, periodically repeated in a cyclic mode. One PSA cycle consists of two main phases: adsorption and regeneration.
Control software ensures sequence of process operations and switching of operating adsorber to maintain product purity. Therefore, sequential execution of operations ensures that before the adsorption capacity of operating adsorber is exhausted, another adsorber will undergo regeneration and will be pressurized to take over the adsorption function.
Figure below explains the pressure swing adsorption process. It shows adsorption isotherms that describe the relationship between partial pressure of the component and its equilibrium loading into the adsorbent for constant temperatures.
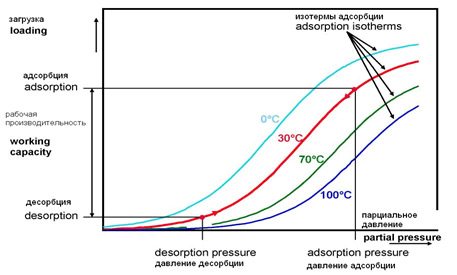
Adsorption is performed under high pressure (usually in the range of 10 - 40 kg/cm2), increasing the corresponding partial pressure and consequently the equilibrium loading of impurities into the adsorbent.
Desorption or regeneration take place under low pressure (usually slightly above atmospheric pressure), reducing the equilibrium loading of impurities into the adsorbent.
The amount of impurities adsorbed in one cycle corresponds to the difference between the adsorption and desorption loads (residual load).
ADSORPTION
Feed gas passes through the adsorber in an upward direction from the bottom to the top and impurities such as CO2, hydrocarbons and CO are selectively adsorbed on the adsorbent surface. Purified product hydrogen gas exits at the top of the adsorber and is supplied to the product header.
Purity of product hydrogen remains constant throughout the adsorption cycle. At the end of the adsorption cycle, impurities begin to accumulate. It means that the adsorber is loaded with impurities and shall be regenerated.
After loading during adsorption sequences, adsorber is regenerated in four main steps:
- pressure in the adsorber is reduced to a low level parallel to the supply flow rate. Parallel depressurization uses adsorber's hydrogen to pressurize or purge other adsorbers;
- pressure in the adsorber is reduced in the direction of counter-flow to residual gas pressure (discharge sequence) to remove impurities from the adsorbent;
- adsorber is purged under residual gas pressure with hydrogen recovered in the adsorbers during the purge sequence or with pure hydrogen gas from hydrogen header to remove residual impurities from the adsorbent;
- adsorber is placed under pressure in steps up to the pressure of hydrogen adsorption of the adsorbers.
Feed gas composition
For continuous process, impurities adsorbed during the adsorption phase shall be removed from the adsorbent bed during regeneration phase. It means that the adhesion forces between the impurity component and the adsorbent shall be high enough for high pressure adsorption, but low enough for low pressure desorption. In order to continuously remove all impurities, PSA units usually have a layered bed, a lower layer (with the lowest adhesive forces) to remove the "heaviest" components, and a top layer to remove the "light" components:
If, for example, due to the difference in composition of feed gas compared to the calculated one, a heavier component is transferred to the upper layer, then this component will be completely adsorbed by this layer, but desorbed poorly and will therefore continuously deactivate this layer.
Roughly, impurities can be divided into 2 groups.
Group 1:
CO, N2, C1, C2, O2, He
Impurities that cannot lead to irreversible overload of adsorption material.
Operation of PSA unit with extremely high concentration of these impurities (compared to the design concentration) can lead to ingress of these impurities into the product hydrogen. Typically, such product contamination can be detected by in-line analyzer and the operator can respond by reducing PSA inlet flow and/or UTILIZATION RATIO. Then adsorption materials can be completely regenerated if the amount of incoming impurities is reduced.
Group 2:
All components not listed in group 1, especially: CO2, C3, C4+, H2O (steam)
Impurities that can lead to irreversible overload of adsorption material. This is possible in the following cases:
- a) Feed gas contains impurities that are not specified in the unit design basis.
In this case adsorber vessel cannot have any corresponding layer for unspecified components.
- b) Content of critical components in the feed gas is higher than design content OR consumption of feed for pressure swing adsorption exceeds its actual maximum capacity.
Performance of the dedicated bed for these components may not be sufficient even without immediate ingress of light components into the product, which can be detected by in-line analyzer.
In all the above cases, critical components will come into contact with the adsorbent layers, from which they are poorly desorbed or not desorbed at all. This results in ongoing deactivation that cannot be immediately detected by product gas analysis. If, after a certain period of time, ingress of light components occurs due to deactivation of lower layers in the bed, this deactivation will most likely be irreversible under PSA conditions and will lead to permanent deterioration of its performance.
Therefore, overloading PSA unit with GROUP 2 impurities shall be avoided in any case.
LIQUIDS shall never enter the gas phase of PSA because they will deactivate the adsorbent layers in any case.
Following diagram shows PSA Unit configuration
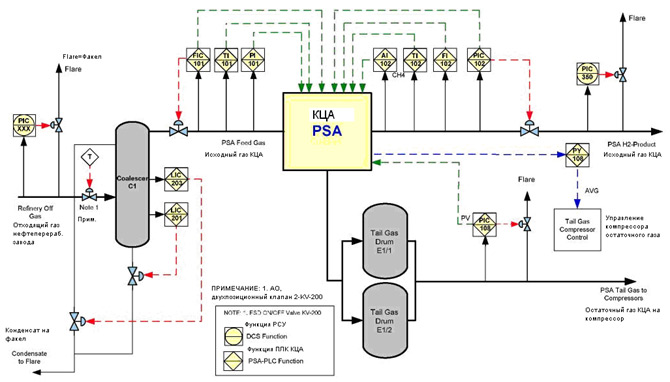